Catalyst is an equal opportunity partner who supports both established and emerging brands. With expertise in direct-to-retail and direct-to-consumer brand strategy, we understand the marketplace and what sells—whether it’s through Amazon, Target, GNC or the local health store. Our custom formulations and flavor profiles offer unique ways to differentiate your brand, and we have an entire team dedicated to ensuring your products are the best they can be.
Executive Team
Andy Kupsco was appointed as CEO of Catalyst Nutraceuticals in June of 2023. Since that time, he has assembled an Executive Leadership team with a proven track record of success in manufacturing.
Brett Anderson, who co-founded Catalyst in 2015, serves as Chief Commercial Officer. Brett is amongst the most knowledgeable and well-connected professionals in the Nutraceuticals Contract Manufacturing space. Importantly, he brings a founders mentality to the leadership team, helping us bridge a successful past to an exciting future.
Mayur Valanju joined as COO in November 2023 having most recently served as the head of R&D and Engineering for Kimberly Clark Professional. At one point in his career, he led the Contract Manufacturing business for Baxter. At Catalyst he is responsible for our Production, Procurement, Quality, Product Development and Customer Service.
Emilio Isom joined as CFO in March 2024 from Amazon Web Services. This is the third time that Andy and Emilio have worked together, previously collaborating at both Honeywell and Cox Automotive. A formally educated Data Scientist, Emilio is responsible for all things Data and Information Technology related in addition to his more traditional Finance responsibilities.
Dr. Marc Zolar was promoted to VP of Human Resources in January 2025. He has an extensive background in training and organizational development, with specific experience in instructional design.
Senior Leadership
The Vice Presidents of Operations, Supply Chain, and Product Development work in close collaboration to ensure that customer products and experiences consistently meet high standards of food safety, quality, and innovation. The VP of Operations teams up with the VP of Supply Chain to ensure smooth logistics and timely delivery while maintaining product quality and safety. At the same time, the VP of Product Development collaborates with both teams to integrate customer insights and innovation into product creation. Through their combined efforts, they deliver products that are crafted to perfection, efficiently delivered, and backed by a white glove service that exceeds customer expectations.
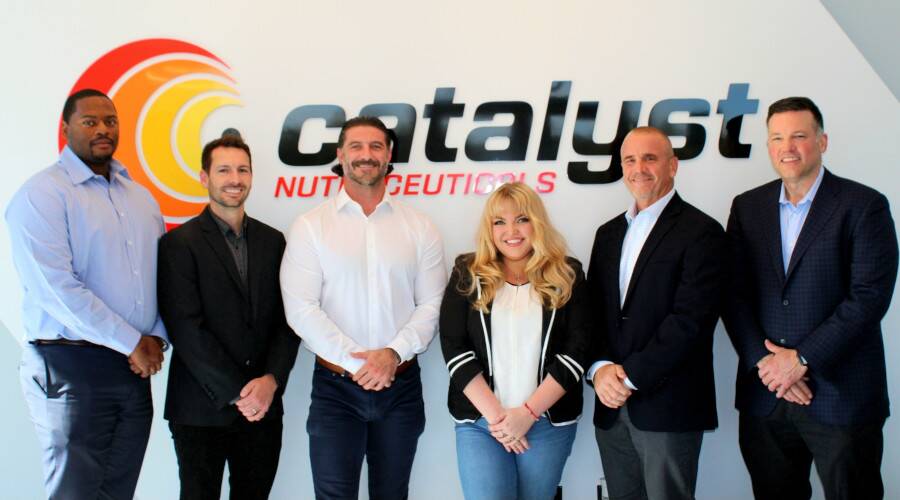
Sales & Marketing
The sales and marketing team at Catalyst Nutraceuticals is a dynamic group dedicated to driving client success and business growth. Combining deep industry knowledge with a client-focused approach, the team excels at understanding unique needs and delivering tailored solutions. They utilize data-driven strategies and innovative campaigns to effectively position Catalyst as a leader in nutraceutical manufacturing. Committed to building strong partnerships, the team ensures seamless communication and exceptional support throughout the entire client journey. Their passion for excellence fuels their ability to consistently exceed expectations and foster long-term success.
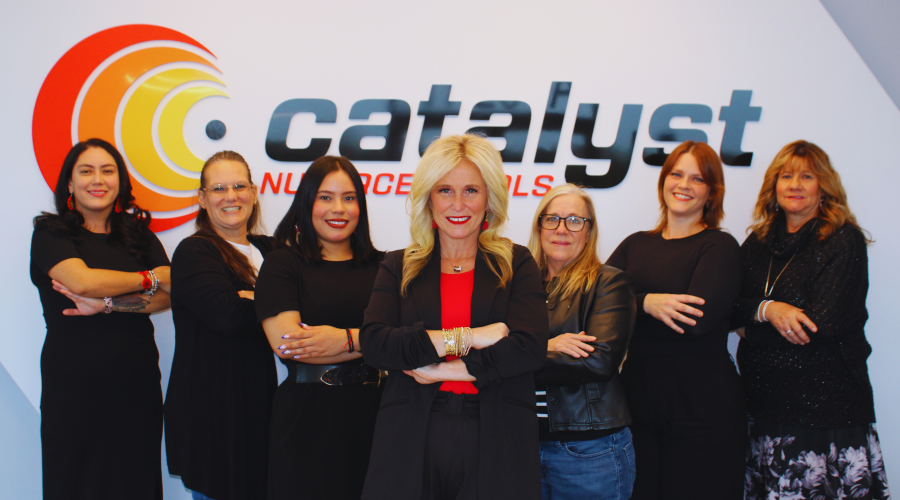
Customer Service
The Customer Service Team's key responsibilities are keeping customers updated on the status of their orders during the manufacturing process. This includes timely updates on the progress of their orders as well as any potential delays and/or issues that may arise during the process. We take over updates after sales orders are placed in the system and follow the orders all the way through the manufacturing and shipping processes.
Product Development
Our product development team plays a crucial role in ensuring quality, innovation, and exceptional service by overseeing the end-to-end process of product creation and delivery. From formulation and ingredient sourcing to rigorous testing, we ensure that each product meets the highest safety, efficacy, and performance standards. Our application team also provides exceptional customer flavor experiences, leveraging innovative flavor concepts and deep ingredient knowledge to create tailored solutions. Our involvement in commercialization and scaling ensures smooth production, while our focus on specification creation and management guarantees consistency and compliance. Additionally, label reviews help provide transparent, accurate information, supporting a seamless customer experience and reinforcing our commitment to white glove service.
Procurement
The Purchasing Department at Catalyst Nutraceuticals plays a vital role in ensuring the seamless flow of high-quality materials required for production. By cultivating strong relationships with trusted suppliers and leveraging strategic procurement practices, the team secures the best pricing, consistent availability, and reliable delivery of materials. Focused on efficiency and cost optimization, the department carefully manages inventory, forecasts demand, and mitigates supply chain risks. Through their dedication to collaboration and innovation, the Purchasing team supports Catalyst’s commitment to delivering superior products and maintaining strong partnerships with both suppliers and customers.
Quality Leadership
The Quality Department at Catalyst Nutraceuticals is dedicated to ensuring the highest standards of quality, safety, and compliance across all aspects of production. Through meticulous inspections, advanced analytical testing, and rigorous adherence to regulatory requirements, the department guarantees that every product meets industry benchmarks and customer expectations. This includes maintaining GMP compliance, conducting third-party audits, and managing supplier quality to ensure robust systems and superior materials. By fostering innovation and continuous improvement, the Quality team delivers safe, reliable, and premium dietary supplements, strengthening customer trust and supporting global regulatory and compliance needs.
QA
The Quality Assurance team serves as the backbone of our dedication to producing superior dietary supplements as a contract manufacturer. Their main goal is to uphold the highest standards of quality, ensuring products align with stringent regulatory guidelines and industry benchmarks. By overseeing each phase of the production process with precision, they guarantee product safety, consistency, and reliability. Their commitment extends beyond quality control, embracing innovation and providing premium, tailored support to meet our customers’ unique needs. This unwavering focus on excellence strengthens customer trust and ensures we deliver outstanding value with every product.
QC
The Quality Control Organization ensures that products meet the highest standards by conducting thorough inspections and testing throughout the production process. Their meticulous attention to detail allows them the ability to identify and resolve any potential issues before they reach the customer. By maintaining strict quality protocols, they help foster innovation while guaranteeing that each product meets both functional and aesthetic requirements. Their dedication to precision and continuous improvement ensures that every product delivered is not only of superior quality but also embodies the innovation and exceptional service that our customers deserve.
Regulatory
Catalyst’s Regulatory Department is here to ensure that our facility, employees, materials, suppliers, and our customers are following all of the appropriate rules and regulations to protect the quality and safety of the products we manufacture. The regulatory piece of this department helps our customers with all sorts of regulatory and compliance needs such as international regulations and registrations for countries like Italy, Mexico, Canada, Australia, France, the Middle East, etc., legal certificates and forms for product compliance, “big box retailers” registrations and much more. Our regulatory department also manages the facility's GMP and third-party audits to verify compliance and safety. Another piece of our regulatory department is our Supplier Quality team who ensure that all the suppliers and manufacturers we do business with are approved, qualified, and have robust Quality systems to provide our customers with best material on the market.
Analytical
Our analytical laboratory specializes in testing nutraceutical products to ensure they meet the highest standards of quality and efficacy. We utilize advanced analytical techniques to assess the potency, purity, and safety of each product, ensuring compliance with industry regulations and customer needs. With a focus on innovation, our team continually explores new methods to enhance testing performance and integrity. Our commitment to quality is to help customers create premium, reliable nutraceuticals that consumers can trust.
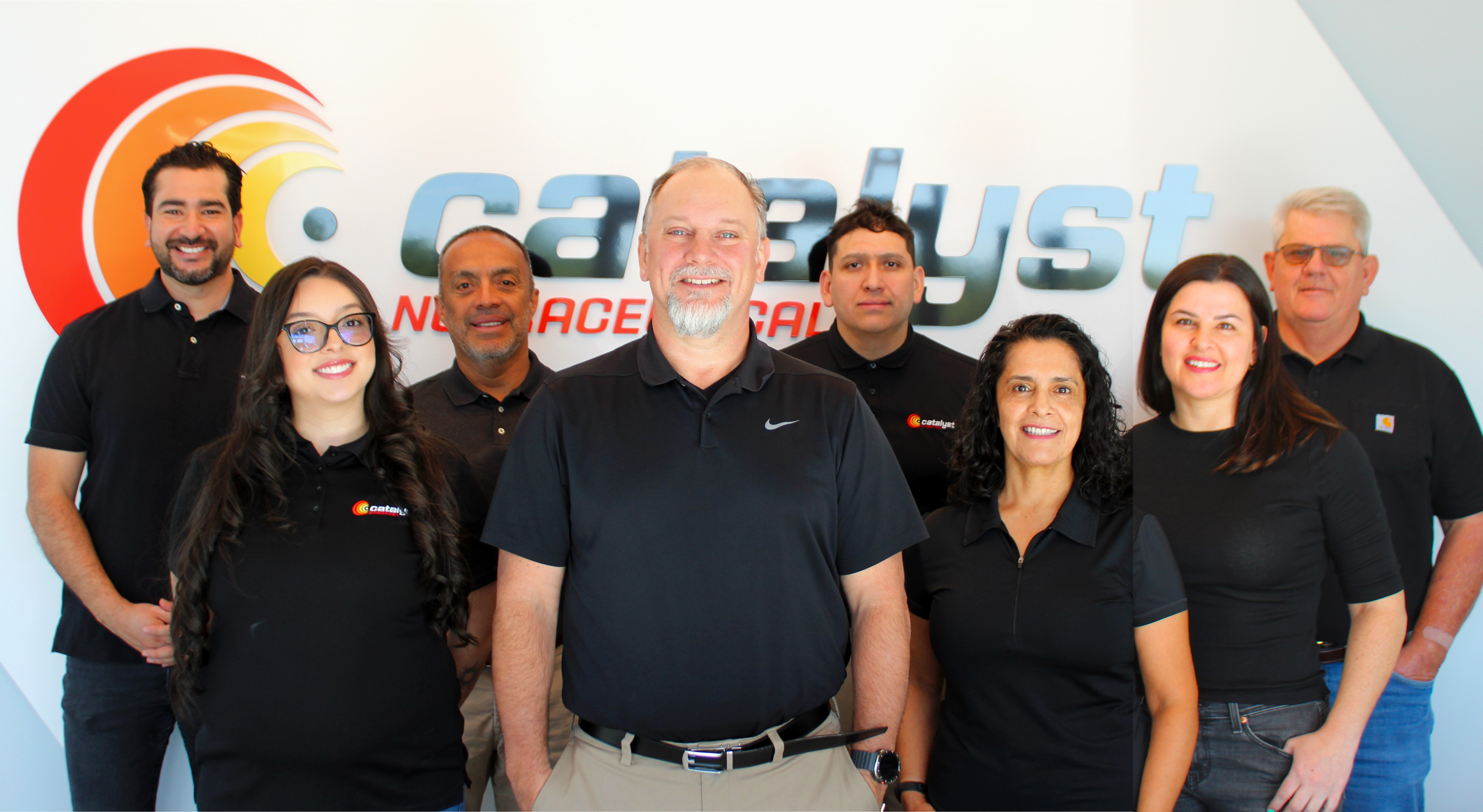
Operations Leadership
Operations leadership is responsible for managing and overseeing the day-to-day business processes of a company, focusing on ensuring product safety and quality by maximizing the equipment and labor efficiency, in order to timely delivery of products to our customers while encompassing a safe work environment. Additionally, this leadership is responsible for bridging strategic goals with tactical execution by directing the operational aspects of the business through a dedicated production team.
Production 1 & 2
The production of nutraceuticals starts with sourcing high-quality raw materials. These ingredients are then processed through methods like extraction and concentration to isolate active compounds. The ingredients are blended into specific formulations, ensuring consistency and quality through rigorous quality control checks. After packaging, the final products undergo testing for purity, stability, and shelf life, all while adhering to Good Manufacturing Practices (GMP) and regulatory standards to ensure safety and effectiveness.
Encapsulation
The encapsulation department is responsible for the process of enclosing substances for nutraceutical purposes. This department plays a critical role in ensuring that products are safe, effective, and meet regulatory and customer standards.
Blend & Sanitation
The blending process in nutraceuticals is a crucial step in the manufacturing of dietary supplements, functional foods, and other health-related products. It involves the uniform mixing of various raw ingredients—such as vitamins, minerals, herbs, amino acids, and other bioactive compounds—into a consistent blend. Typically, blending begins with the careful selection of ingredients, followed by precise measurement and batching. The raw materials are then added into a mixing vessel to ensure an even distribution. The blending process may vary depending on the physical properties of the ingredients (e.g., particle size, density, and flowability) to avoid issues like segregation or clumping. Once the blending process is complete, the mixture is ready for subsequent steps, such as encapsulation or powder filling, depending on the product type.
The sanitation process in nutraceuticals involves cleaning, disinfecting, and maintaining hygiene in the manufacturing environment to ensure the safety and quality of the products. Key responsibilities include preventing contamination, compliance, maintaining equipment, health and safety, ensuring product quality, and documentation. In summary, the sanitation team is crucial for ensuring cleanliness, regulatory compliance, and the overall safety of products and workers in the facility.
2nd Shift
The second shift in nutraceutical production focuses on maintaining smooth operations and consistency in quality throughout the day. During this shift, the same rigorous processes are followed as in the first shift. Raw materials are processed into active ingredients through extraction, concentration, and other methods. Formulations are blended, ensuring uniformity and potency, with quality control teams conducting inspections at every stage.
In addition to regular manufacturing tasks, the second shift emphasizes continued monitoring of equipment, maintaining sanitary conditions, and ensuring compliance with Good Manufacturing Practices (GMP). Finished products undergo final testing for purity and stability, while inventory is updated for accurate tracking. The second shift ensures that production runs seamlessly, without interruption, to meet demand and deliver high-quality nutraceutical products.
Warehouse
The warehousing and logistics focuses on the safe and efficient handling, storage, and distribution of all incoming materials and outgoing finished products while ensuring compliance with industry regulations. Upon receipt, raw materials and ingredients undergo a thorough inspection for quality. These materials are then stored to avoid commingling of different classes of materials with stock rotation following FEFO (First Expired First Out). When finished goods are packaged and labeled according to the FPS, shipping is responsible for loading and shipping the materials following proper transportation conditions. Throughout the entire process, adherence to Good Manufacturing Practices and other regulatory standards is maintained to ensure product traceability.
Engineering
The maintenance department is responsible for ensuring the proper functioning of equipment through regular maintenance and timely repairs. It oversees facility upkeep, manages inventory, and conducts safety inspections to ensure compliance with regulations. The team also provides training and education to staff, maintains accurate documentation and records, and develops budgets to control costs effectively. These responsibilities ensure the smooth operation and safety of the organization.
Finance
The Finance department is a strategic partner to the business providing insights and data that help shape customer-focused strategies. In addition to evaluating, recommending, and approving critical investments in the business, the team allocates resources to initiatives that enhance the business’s ability to scale and enhance customer satisfaction. We have a focus on improving technology platforms, and leading continuous improvement efforts in our most critical business processes.
Human Resources
The Human Resources team collaborates with all departments across the company to support the full scope of HR activities, including hiring, onboarding, performance management, benefits administration, organizational design, employee engagement programming, training and development, and compliance with federal, state, and local regulations. The team is led by the Vice President of Human Resources and includes a Sr. HR Manager and an HR Generalist who work closely with the company’s leadership on strategic initiatives while also servicing the day-to-day needs of our employees. Key initiatives include labor forecasting and management, compensation and benefits analysis, annual and mid-year performance review cycles, employee engagement surveys, and training curriculum development and administration.